一、一体化压铸将成为新能源汽车的发展趋势
一体化压铸的定义:一体化压铸是将汽车部件的铸铝化及集成化。其工艺特点是通过大吨位压铸机制造大型铝制零部件,主要指汽车车身结构件一体化加工,将原本设计中多个单独、分散的小件经过重新设计高度集成,再利用压铸机进行一次成型压铸成完整零件(省略焊接及组装流程)。此外,新能源车三电系统等多合一壳体也引入一体化压铸技术来实现集成制造。大型一体化压铸主要适用于乘用车下车身,包括后地板、前地板及前机舱、电池盖以及白车身等。 新能源汽车带来了一体化压铸市场的强劲需求,以特斯拉为引领,新势力造车企业跟进,传统汽车制造企业转型,为未来的一体化压铸市场带来了想像空间。 当前一体化压铸变革主要应用于新能源汽车车型开发,其中造车新势力功不可没。特斯拉率先采用一体化技术,蔚来、小鹏、理想、小米、高合紧随特斯拉布局一体化压铸。 传统“冲压+焊接”模式是传统造车企业制造的主流,其切换速度仍比新能源车企业慢,做出样件要耗时半年以上。2022年2月沃尔沃是第一家公告拟投资一体式压铸工艺的传统车企。其后大众汽车3月表示,已在德国沃尔夫斯堡-瓦尔梅瑙其主要工厂附近建立一个新生产基地,将引入一体化压铸工艺。国内主流汽车厂一汽、长安、吉利、长城也在积极布局一体压铸,预计今年可完成样件生产。
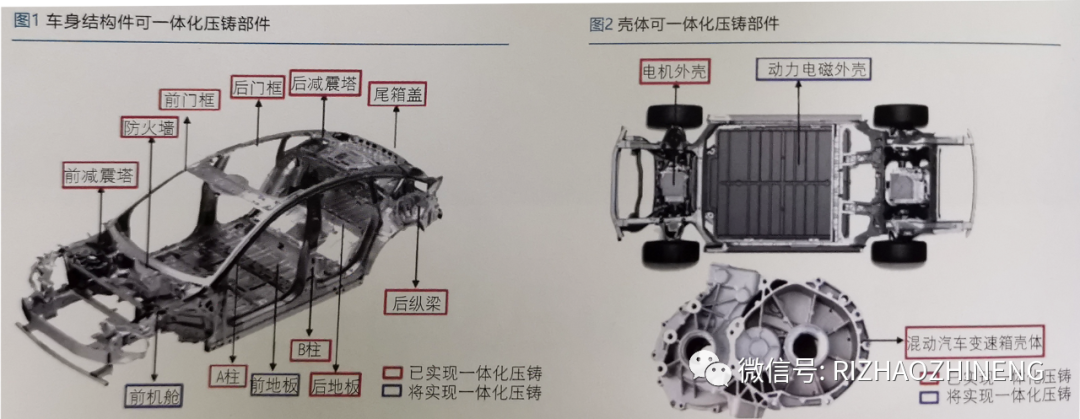
目前可以量产的一体化车身部件是特斯拉。其后地板率先量产,前舱体紧随其后,降本增效显著。特斯拉是目前唯一实现后底板一体化压铸量产的主车厂。2020年9月22日,马斯克在特斯拉电池日发布会上介绍称Mode1 Y将采用一体式压铸后地板总成,铸造零件可以从此前的70个简化到2个,未来可能会合为1件。车身结构稳定性和轻量化得到大幅优化,同时还减少近1000次的焊接工序,节省约20%的生产成本。 后地板率先一体化压铸原因主要有以下几方面,1)后地板碰撞受损的几率小,安全性能要求相对其他下车体稍低;2)6000T大型压铸机可以满足后地板制造条件,更大零部件设备正在研发;3)一体化压铸后地板较传统焊接工艺刚性更优,可更好兼顾底盘操纵性能。 国内新势力一体压铸布局中,蔚来汽车量产在即,小鹏汽车完成打样,理想汽车完成打样,小米汽车完成一体化压铸设备采购。 传统汽车企业中的吉利汽车完成一体化压铸设备采购,长安汽车、一汽正在进行一体化压铸设备采购前的准备工作。 蔚来汽车布局一体化压铸。2021年10月18日,蔚来宣布成功验证开发了可用于制造大型压铸件的免热处理材料,全新材料将会应用在蔚来第二代平台车型上,12月18日,蔚来在NIODay上发布,全新车型ET5的车身后地板相关部件将采用一体式铸造成型,使车身后地板重量降低30%,同时后备箱空间增加11L。 小鹏汽车布局一体化压铸。武汉工厂加入了一体化压铸工艺车间,武汉工厂将引进二套(条)以上超大型压铸岛及自动化生产线。1月18日,小鹏宣布与广东鸿图签约12000吨超级智能压铸单元,以及新能源汽车 一体化前舱总成、一体化后地板总成和一体化电池托盘等关键和核心轻量化部件等项目。
轻量化及提效降本需求推动一体化压铸
减重:特斯拉计划用2-3个大型压铸件替代原先370个零件组成的下车体总成,重量将降低30%。 降本:特斯拉后地板替换的成本下降在20%左右。实现下车身一体化后,制造成本下降40%。 提效:采用了一体式压铸后地板总成的Mode1 Y,用1-2件大型压铸件替换了原来的70个零件,焊点大约由700-800个减少到50个。制造时间由传统工艺的1-2小时缩减至3-5分钟,可实现在厂内直接供货。
二、产业链各环节空间与格局分析
随着一体化压铸技术的成熟,前机舱、前地板、后地板、上车身结构件均实现一体化压铸,需要2台6000t、1台9000t、1台12000t压机,单车价值量12200元;2)全球乘用车销量达到10000万辆,中国乘用车销量达3000万辆,一体化压铸渗透率50%;3)压铸机规划产能10万套/台,产能利用率70%,良率90%,设备更换周期10年,6000、9000、12000t压铸单元价格分别为5000、7500、10000万元;4)免热处理铝合金单价18元/kg;5)模具一年更换一次,6000t、9000t、12000t压铸机对应模具单价分别为500、600、700万元。
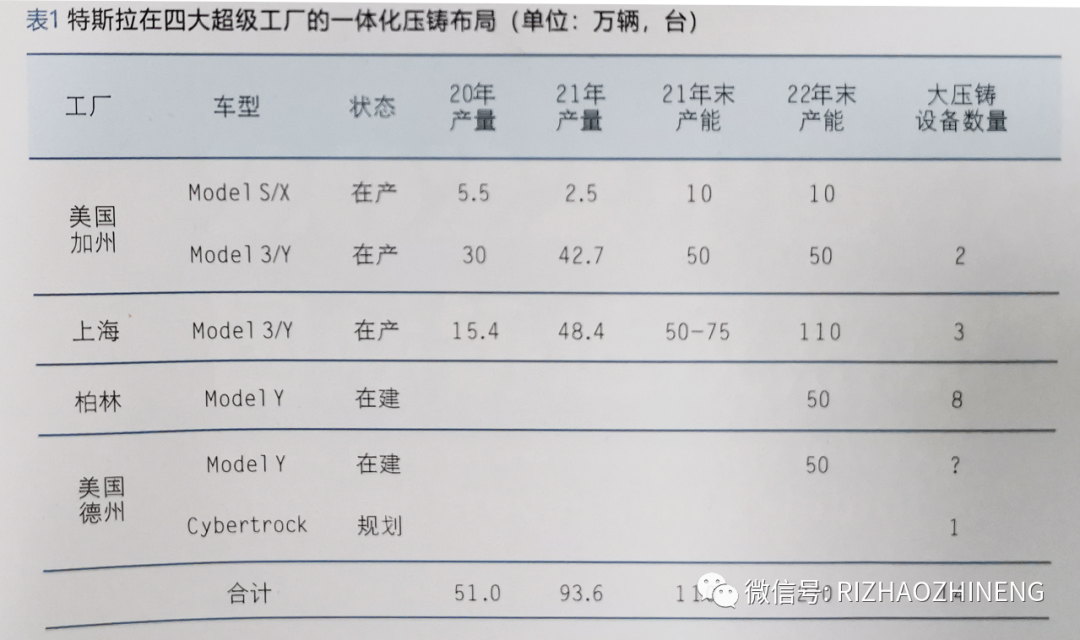
预计到2025年,一体化压铸车身结构件市场空间分别有望达到376.7亿元,复合增长率160%;大型压铸机市场空间分别有望达到50亿元,复合增长率90%;免热处理铝合金材料市场空间有望达到161.3亿元,复合增长率139%;模具市场空间有望达到10.9亿元,复合增长率131%。产业链各环节均有翻倍及以上的增速,其中一体化压铸车身结构件增速最快。 单车价值量按1)前机舱2200元、前地板3500元、后地板2000元;2)2023年前机舱实现量产,2024年中地板实现量产。 未业,一体化压铸车身结构件市场全球及中国市场空间分别有望达到6100和1830亿元;大型压铸单元全球及中国市场空间分别有望达到218.3和65.5亿元;免热处理铝合金材料全球及中国市场空间有望达到2500和750亿元;模具全球及中国市场空间有望达到182.5和54.8亿元。
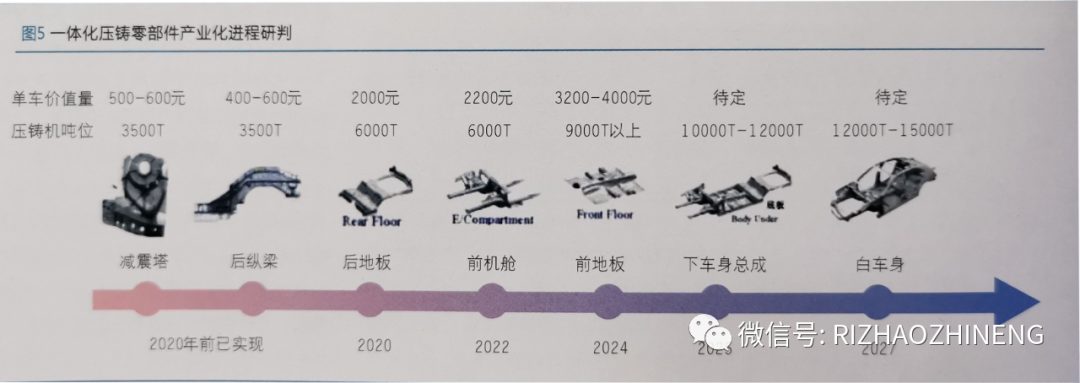
大吨位压铸机格局分析
大型压铸机主要玩家有老牌瑞士厂商布勒、国内上市公司龙头力劲科技、伊之密,以及海天集团子公司海天金属等。瑞士布勒、中国力劲以及海天是目前具备规模量产6000吨以上大型压铸机的制造商。
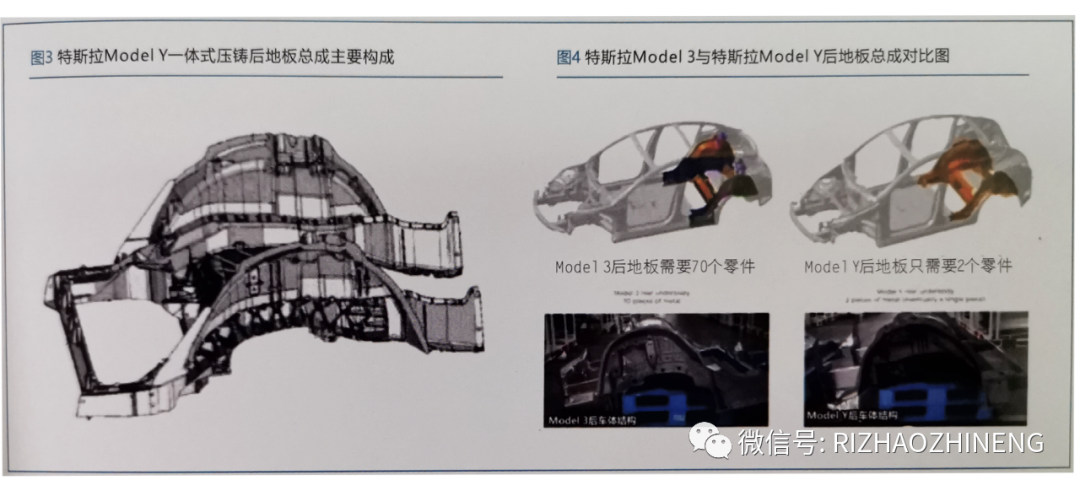
力劲科技及子公司意德拉率先量产6000t压铸机并供货特斯拉。根据意德拉官网产品介绍,在合模力、压射力、模板 尺寸、射料量上均有明显突破。2021年力劲发布9000吨大型压铸机,将压铸机的吨位再向前推进一步。12000t压机正在与广东鸿图等公司合作研发。布勒在21年初发布6100t压铸机,预计在2022年发布9000t压铸机;海天金属8800t压铸机也已完工交付美利信。
一体化压铸铝合金材料格局分析
国内一体化压铸铝合金材料格局是国外技术领先,国内迅速跟进。 1985年,在德国汉诺威展会上,两名身材苗条的女子毫不费力地举起了奥迪100的全铝车身,推开了车身轻量化的第一道任意门。在此之前,铝合金主要是用在航空领域,它的成分一度被德国视为国家机密,之后才慢慢走入了汽车领域。相比于传统的低碳铁,铝合金要轻三分之一,伸缩性和可塑性更好,能够在发生碰撞的时候更好地吸收溃缩(即通过变形分散碰撞动能)。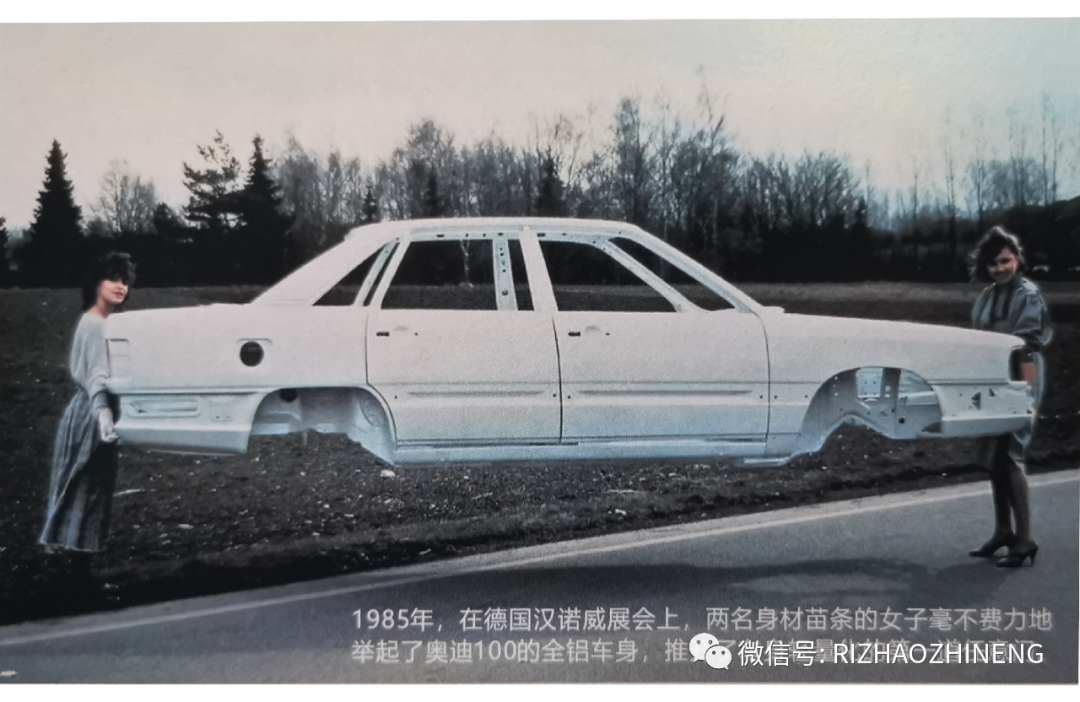
然而,一种新材料想要被量产车所接纳,只是性能出色还不够,换了新的材料就需要新的工艺或者结构,只有三者配合默契才能实现“质量-成本-性能”之间的平衡。 对于传统铝合金而言,热处理是保障压铸零部件机械性能的必备手段,热处理过程易引起汽车零部件尺寸变形及表面缺陷,由于一体化压铸零部件较大,因此后期再进行热处理将产生较大程度变形,因此需要使用免热处理铝合金材料。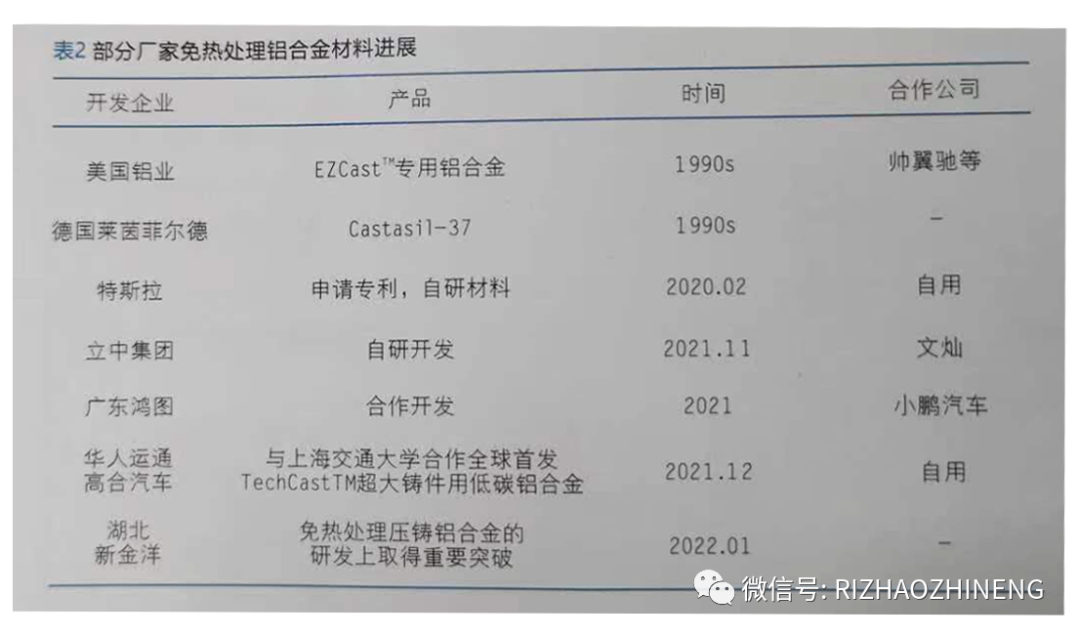
免热处理铝合金国外有美国铝业、德国莱茵公司,国内有立中集团、帅翼驰、上海交大等,具体见上表。
一体压铸模具格局分析
国内一体压铸模具目前主流趋势是主机厂与供应商合作共进。 目前一体化压铸车身结构件模具进展较快的主要有:广州型腔、宁波臻至以及宁波赛维达。其中广东型腔已经为美利信配套8800t超大型压铸机一体化后地板压铸模具,与鸿图、力劲以及广东鸿劲签署了《12000吨超级智能压铸单元联合研发合作协议》,共同就12000T(吨)超级智能压铸单元开发项目开展合作。宁波臻至模具为宁波海威开发了前舱体一体压铸模具。宁波赛维达为特斯拉、拓普开发了车身一体压铸模具。
国内一体压铸企业未来格局分析
国内一体压铸企业初期格局将以整车厂自制和外部压铸企业供应并存。
特斯拉率先采用一体化技术,蔚来、小鹏、理想紧随特斯拉布局一体化压铸,传统主机厂中如吉利、大众、沃尔沃、比亚迪、长安等也有相关入场计划。特斯拉后地板、前舱体已经实现量产自制,小鹏汽车以自制与外部压铸企业供应同时进行。理想和蔚来或主要依托外部零部件厂商。预计中期格局会因重资产低周转属性导致外部一级供应压铸企业主导更占优。 长期来看,一体化压铸属于重资产的领域,压铸单元单条生产线投资近一亿元,而年产能只有6-8w套。据测算,在良率达到90%时,投入产出比仍高达1:2;毛利率在37%左右。而主机厂的固定资产周转率较高,广汽和长城等主机厂长期保持在3以上,可以看出其经营特点并非重资产。因此,短期主机厂尤其是特斯拉和小鹏等新势力出于保供压力以及外部一级供应压铸企业能力未普遍成熟时期亲自涉足,但是长期看一体化压铸资产较重,后期在产能充足以及工艺逐步成熟后将由外部压铸企业主导。